Produits d’excellence pour qualité et continuité, grâce au passage aux fours à induction
Nous étions en pleine pandémie lorsque nous avions entamé notre transformation. Il a fallu beaucoup de courage pour faire face à un engagement économique, significatif pour nous, sans savoir où nous mènerait l’effet d’un confinement qui perdure et dont on ne voit pas la fin. Avec un peu d’audace et une bonne dose d’optimisme nous sommes allés de l’avant, aussi parce que nous avions pris un engagement avec le fournisseur des fours et le mot est le mot: le respect s’impose en toutes circonstances, même dans les plus impensables.
Mais le plus gros engagement que nous avions pris était avec certains clients qui attendaient cette étape pour l’amélioration évidente que nos produits auraient obtenu.
La décision de passer à l’induction électromagnétique a en effet été prise quelques mois avant le déclenchement de la pandémie en Italie.
Jusqu’en 2020 à l’I.S.A.C. nous utilisions des fours à gaz méthane pour chauffer l’acier et avant cela, jusqu’en 2008, avec de l’huile dense.
L’avantage de ce nouveau système de chauffage est une température plus homogène de la pièce et en même temps moins de scories, ainsi qu’un contrôle total du processus de chauffage qui se traduit à la fois par la qualité et l’efficacité énergétique.
Au-delà des difficultés rencontrées, comme la disponibilité de l’électricité (il a fallu construire une nouvelle sous-station électrique et attendre que le courant soit disponible dans le réseau de distribution) mais aussi une livraison retardée des fours en mai 2020 (le coronavirus pourrait pas d’impact sur aucun secteur), les avantages ont été immédiatement évidents.
Au niveau du processus, l’impact a été:
- une réduction significative des scories, ce qui dans le processus avec le four à gaz était vraiment remarquable. Non plus de décisions comme « rajoutons un peu plus de matière pour compenser ce qui abîme la scorie »;
- l’absence totale de temps morts en pré et post-traitement, une plus grande rapidité de réponse à toute variation de température requise, une reproductibilité rigoureuse des paramètres opératoires, une automatisation aisée de l’ensemble de la ligne et donc une adaptabilité plus aisée aux multiples besoins de production: enfin notre procédé est devenu pleinement sous contrôle.
Mais surtout les avantages se sont immédiatement manifestés sur le produit: notre client majeur a immédiatement exprimé le besoin d’homologuer ce type de chauffage, compte tenu de la transformation radicale de cette phase vitale de notre travail. Faits – à distance, compte tenu de la pandémie en cours – avec des analyses structurelles sur les pièces à chaque étape de leur traitement, les rapports finaux du laboratoire ont donné d’excellents résultats, avec une approbation totale.
Aujourd’hui, I.S.A.C. consomme près de 1 gigawatt par mois, dans le respect du cahier des charges des clients et de leur satisfaction et, sans oublier, achète de l’électricité à des fournisseurs qui la produisent par plus de 40 % de sources renouvelables.
Parce que on peut aussi gagner en efficacité tout en respectant l’environnement.
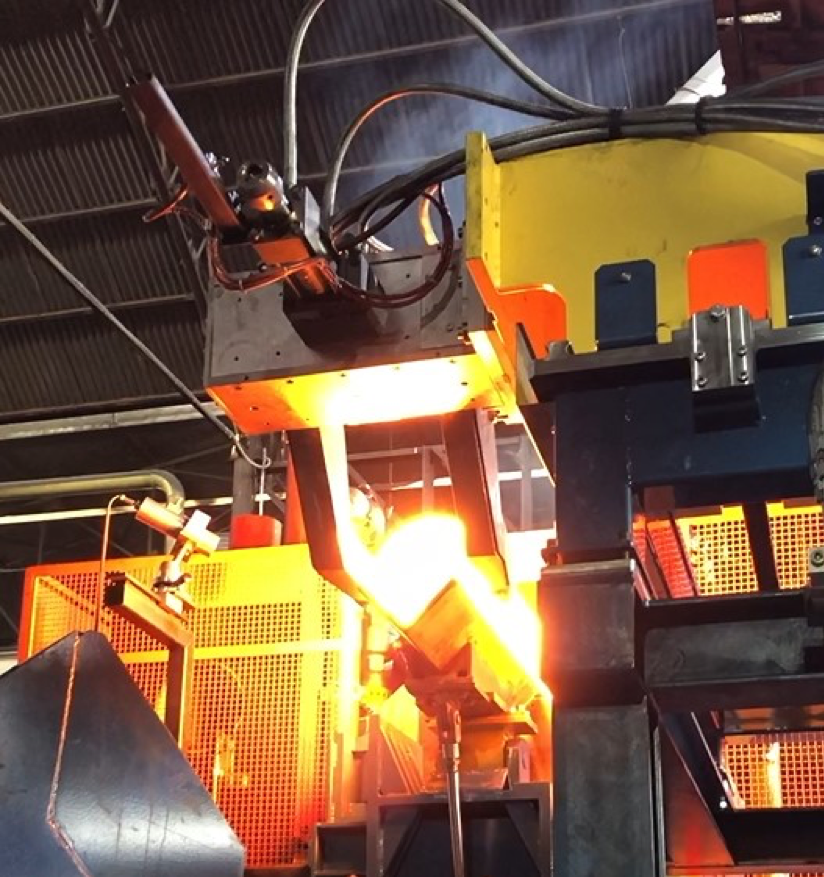