Prodotti eccellenti per qualità e in continuità, grazie alla svolta verso i forni a induzione
Eravamo in piena pandemia quando abbiamo avviato la nostra trasformazione. C’è voluto tanto coraggio ad affrontare un impegno economico, notevole per noi, senza sapere dove ci avrebbe portato l’effetto di un lockdown che continuava a protrarsi e non se ne vedeva la fine. Con un po’ di sfrontatezza e una buona dose di ottimismo siamo andati avanti, anche perché avevamo preso un impegno con il fornitore dei forni e la parola è parola, il rispetto va dimostrato in ogni circostanza, anche in quelle più impensabili.
Ma l’impegno più grosso l’avevamo preso con alcuni clienti che attendevano questo passaggio per l’evidente miglioramento i nostri prodotti ne avrebbero ottenuto.
La decisione di passare all’induzione elettromagnetica era stata infatti presa qualche mese prima dello scoppio della pandemia in Italia.
Fino al 2020 in I.S.A.C. utilizzavamo per il riscaldo dell’acciaio forni a gas metano e prima ancora, fino al 2008, a nafta densa.
Il vantaggio di questo nuovo sistema di riscaldo è una temperatura più omogenea dello spezzone e al contempo una minore scoria, oltre ad avere il totale controllo del processo di riscaldo che si traduce sia in qualità che nell’efficientamento dei consumi.
Lasciando in secondo piano le difficoltà incontrate, tipo la disponibilità dell’energia elettrica (fu necessario costruire una nuova cabina elettrica ed attendere che la corrente fosse disponibile nella rete di distribuzione) ma anche una consegna dei forni ritardata a Maggio 2020 (il coronavirus non poteva che impattare su qualsiasi comparto), i benefici furono immediatamente evidenti.
A livello di processo, l’impatto è stato:
- una riduzione drastica della scoria, che nel processo con il forno a gas è decisamente notevole. Quindi stop a decisioni come “Mettiamo un po’ più di materiale per compensare quello che danneggia la scoria”;
- la totale assenza di tempi morti pre e post lavorazione, maggiore rapidità di risposta ad ogni variazione di temperatura richiesta, rigorosa riproducibilità dei parametri di funzionamento, facile automazione dell’intera linea e quindi più semplice adattabilità alle molteplici esigenze produttive: finalmente il nostro processo diveniva pienamente sotto controllo.
Ma soprattutto i vantaggi furono immediatamente evidenti sul prodotto: il nostro maggiore cliente ci manifestò subito l’esigenza di omologare tale tipo di riscaldo, vista la trasformazione radicale in questa fase vitale del nostro lavoro. Fatta – da remoto, considerando la pandemia in corso – con analisi strutturali sui pezzi in ogni fase della loro lavorazione, i rapporti di laboratorio finali diedero risultati eccellenti, con la piena approvazione.
Oggi I.S.A.C. utilizza quasi 1 gigawatt al mese, nel pieno rispetto dei capitolati dei clienti e della loro soddisfazione e, cosa non da tralasciare, acquista l’energia elettrica da fornitori che la producono utilizzando, per oltre il 40%, fonti rinnovabili.
Perché si può fare efficientamento anche nel rispetto dell’ambiente.
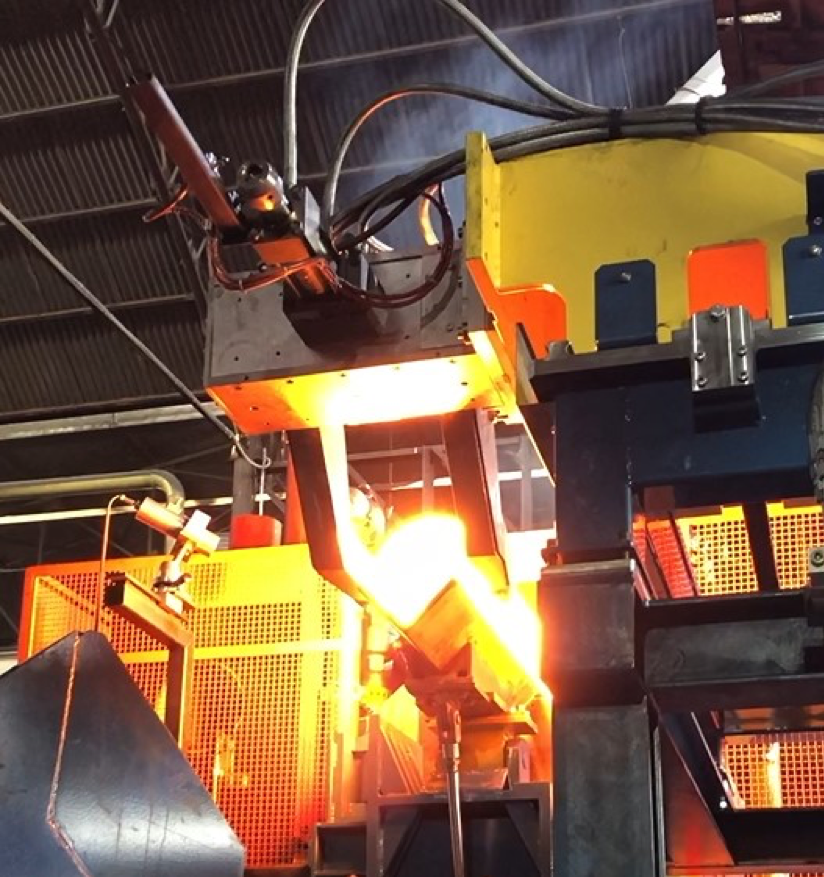