Our excellence in forging also passes through the adoption of induction ovens
We were in full pandemic when we started our transformation.
It took a lot of courage to face an economic commitment, significant for us, without knowing where the effect of a lockdown that continued to last and there was no end in sight would lead us. With a little boldness and a good dose of optimism we went ahead, also because we had made a commitment with the supplier of the ovens and the word is the word, respect must be shown in all circumstances, even in the most unthinkable.
But the biggest commitment we had made with some customers who were waiting for this step for the obvious improvement our products would have obtained.
The decision to switch to electromagnetic induction was in fact taken a few months before the outbreak of the pandemic in Italy.
Until 2020 in I.S.A.C. we used methane gas ovens for heating steel and before that, until 2008, with dense oil.
The advantage of this new heating system is a more homogeneous temperature of the piece and at the same time less slag, as well as having total control of the heating process which translates into both quality and fuel efficiency.
Leaving behind the difficulties encountered, the benefits were immediately evident.
At the process level, the impact was:
– a drastic reduction of slag, which in the process with the gas oven is decidedly remarkable. So stop with decisions like “Let’s put a little more material to compensate for what damages the slag”;
– the total absence of pre and post processing dead times, greater speed of response to any required temperature variation, rigorous reproducibility of the operating parameters, easy automation of the entire line and therefore easier adaptability to multiple production needs: finally our process became fully under control.
But above all the advantages were immediately evident on the product: our major customer immediately expressed the need to homologate this type of heating, given the radical transformation in this vital phase of our work. Done – remotely, considering the pandemic in progress – with structural analysis on the pieces at every stage of their processing, the final laboratory reports gave excellent results, with full approval.
Today I.S.A.C. uses almost 1 gigawatt per month, in full compliance with customer specifications and their satisfaction and, not to be overlooked, purchases electricity from suppliers who produce it using, for over 40%, renewable sources.
Because you can also improve efficiency while respecting the environment.
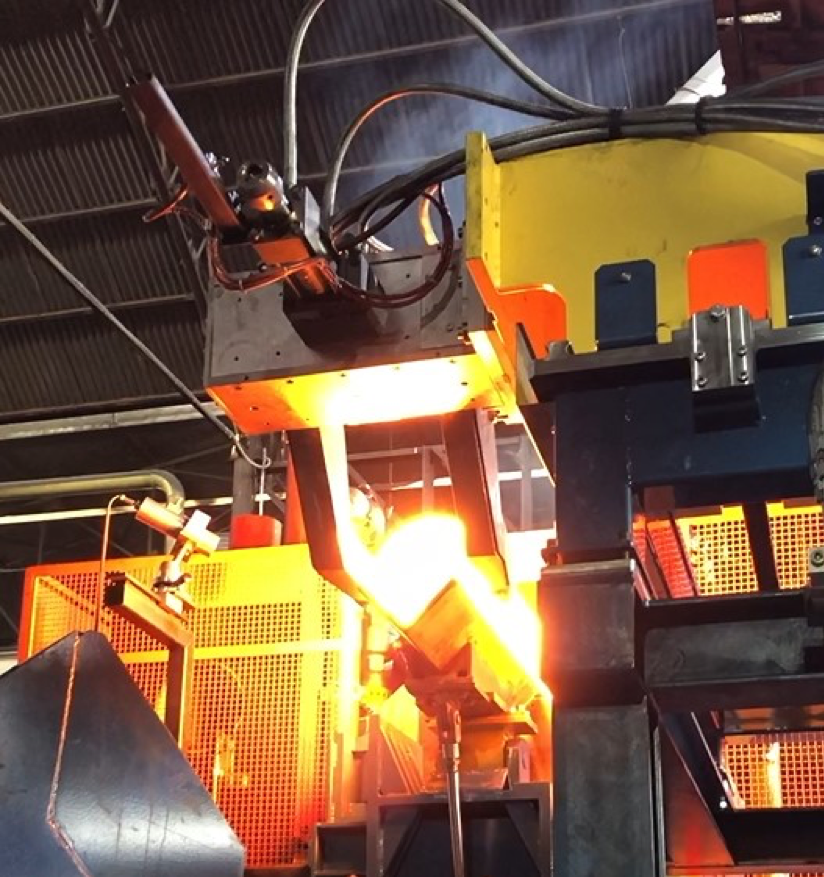